
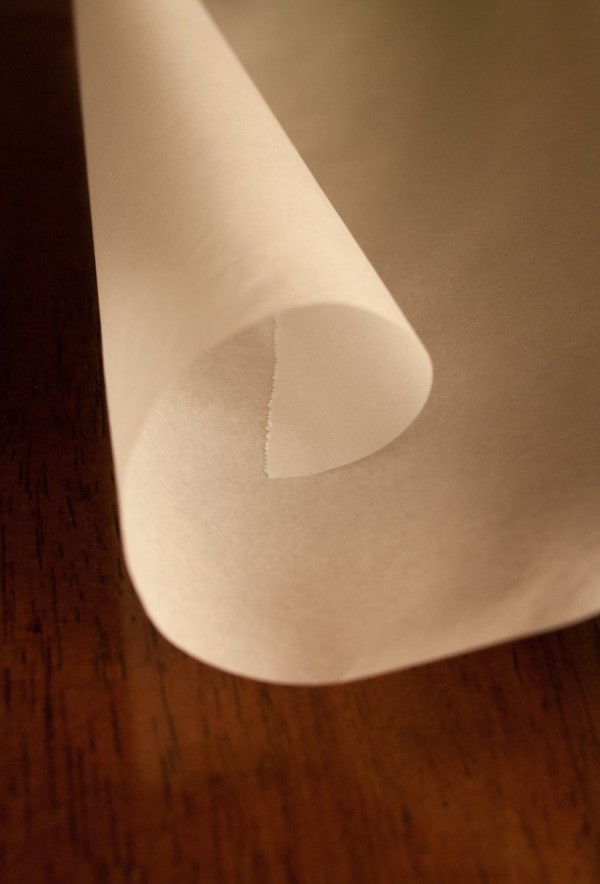
If you keep the thickness under 3/8 inch or so and keep it even throughout, your model can be cast in bronze using the lost-wax method. For a finer finish, use a nylon stocking. These lines may be removed and the surface further smoothed by rubbing with a Scotchbrite abrasive non-woven pad dampened with some mineral spirits or kerosene.
#Brown wax paper series#
These leave a series of fine raised lines on the surface which graphically show any depressions that otherwise might escape the eye. You can also buy sets of toothed scrapers which are designed for smoothing out the contours of plaster models. Loop tools and steel “ribs” such as are used for sculpting clay may be used, as may all sorts of improvised tools. If you don’t have one of these, use an alcohol lamp to heat a steel tool, which will melt a little wax before it cools and must be reheated. Once it cools, it can be worked with tools, or you can use an electrically heated tool similar to a soldering iron (but not as hot) to weld it to itself. Once you have cast sheets of wax 1/8-1/4 inch thick, you can use it more or less like clay, warming it in your hands or using a hair-dryer to warm larger pieces. While sculptors have used beeswax its pure form for millennea, it works better as a component in an alloy. This makes it somewhat more malleable and gives it a nice smell. I like to put some beeswax into the mix about 25% by volume. Wear protective gear when pouring the wax, especially some rubber gloves and a face shield-this stuff can give you some nasty burns, just like deep fat frying. Spilled wax can make a big mess very quickly, and it is very difficult to clean up wax completely when it has spilled.

This is a messy process, so think twice before doing this in your kitchen. If it starts smoking this is not only bad for you, but the next thing you know you have a tower of flame where your wax used to be (and even if you don’t burn down your place, the carbon ruins the wax.). Never melt wax directly over an open flame-if that’s all you’ve got, use a double boiler. The wax can be dipped out of the fryer kettle with smaller pouring containers-I make my own by adding handles to steel cans. It is best to get a fryer with an infinite range control, instead of low, medium, and high settings and check it with a candy/frying thermometer to make sure it doesn’t get too hot. Melt the wax chunks in an electric frying kettle, making sure you keep the temperature under about 225 degrees Farenheit (it will melt considerably lower). Make sure you’re doing this in a clean place you don’t want to get debris in your wax if you can help it. Thinner sheets of wax may be obtained by tilting the mold thicker ones by filling the mold and letting it set.You can break up the ten-pound block of wax by hitting it sharply with a hammer (if it isn’t too warm out). Soak any plaster molds thoroughly in water before pouring melted wax into them this will keep the wax from soaking in and sticking. This can be a simple one-piece mold of any flat smooth object, such as a plastic cutting board. To use it directly, it’s best to make yourself a slab mold, either with rubber or plaster. “Machineable” waxes are similar, but are more forgiving of welds, and permit remelting. These often have a little polyethylene added to make them less sticky but they won’t bend, and are difficult to weld. There are also waxes formulated for carving rather than casting or modeling with the fingers. These can also be alloyed with the softer waxes to produce wax of an intermediate hardness. Another is a pink wax sold in stick form for use as sprues. There are harder waxes, such as Sierra Red, which are suitable for casting into molds, and will retain their shape better than the softer ones.

For even greater malleability, you might try the type of soft wax used to coat cheese. If you are working in an unheated studio in the winter, it might be preferable, but complicated pieces can collapse in the summer if it gets too hot. If you need a more malleable wax, there is also a “Victory Amber” which is similar but softer. Called “Victory Brown”, the type we get here is suitable for hand-modeling if you get it slightly warm, or for casting into molds. Unlike paraffin, it also burns out without leaving an ash residue. It is a “microcrystaline” wax, which means it will bend a lot more readily than paraffin, the white wax used for making candles. In Alt.Sculpture FAQ, Casts and Molds, Concrete and Plaster, Fabrication, Jewelry, Sculpture, Toolsīrown sculpting wax is the basic all-purpose type favored by many sculptors.
